Introducing Loom OS: The Operating System for Modern Apparel Manufacturing
Anatar unveils its proprietary software platform designed to orchestrate and optimize apparel production
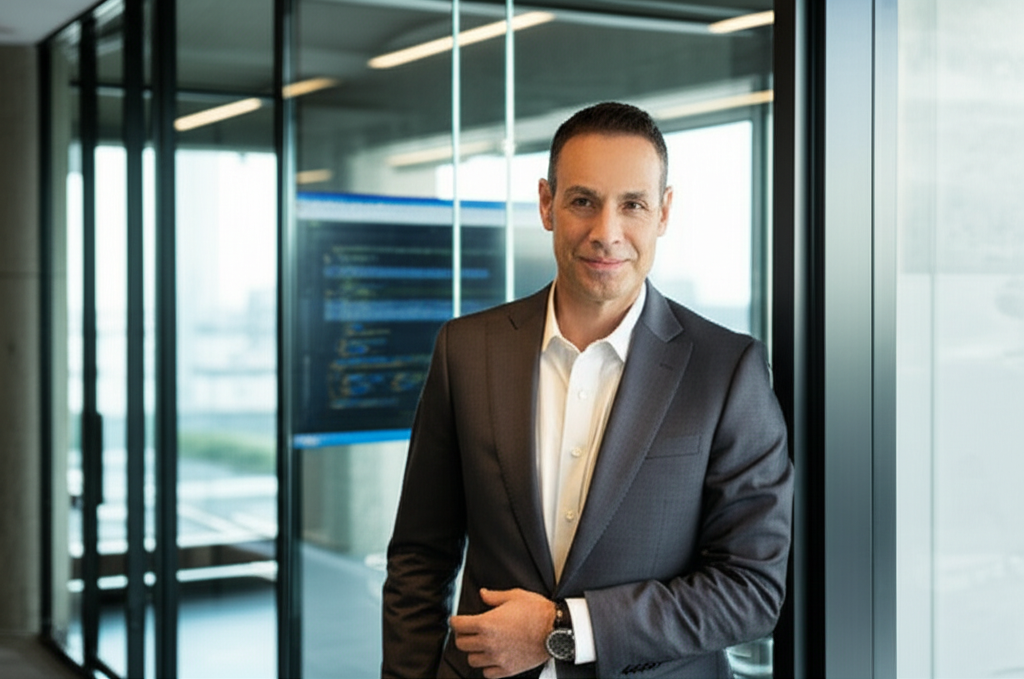
Michael Chen
Chief Technology Officer
Anatar today announced the launch of Loom OS, a groundbreaking software platform designed to orchestrate and optimize every aspect of modern apparel manufacturing. This proprietary system represents a fundamental rethinking of how apparel production is managed, moving from static, siloed systems to a dynamic, integrated platform that enables unprecedented levels of efficiency and visibility.
"Loom OS is to traditional manufacturing software what modern cloud platforms are to legacy enterprise systems," said Michael Chen, CTO of Anatar. "We've built it from the ground up to address the specific challenges of apparel manufacturing in a connected, automated environment."
The platform consists of four integrated components, each addressing a critical aspect of the manufacturing ecosystem:
Loom Core: The Foundation
At the heart of the system is Loom Core, a modern reimagining of SCADA (Supervisory Control and Data Acquisition) systems for autonomous manufacturing. Unlike traditional SCADA systems that simply monitor equipment, Loom Core actively orchestrates production across multiple machines and processes.
"Traditional manufacturing systems were designed for human operators to monitor machines," explained Chen. "Loom Core inverts this paradigm—it's designed for machines to be orchestrated by software, with humans providing strategic oversight."
The system integrates with robotic cutting systems, automated sewing stations, and material handling equipment to create a cohesive production environment. Real-time data from every machine feeds into a central system that can identify bottlenecks, predict maintenance needs, and optimize throughput.
Loom Flow: Dynamic Production Routing
Building on the foundation of Loom Core is Loom Flow, which handles dynamic routing across factory lines based on real-time demand signals. This component uses machine learning algorithms to determine the optimal production sequence and routing for each order.
"In traditional manufacturing, production planning is done weeks or months in advance, and it's difficult to adapt to changes," said Amara Washington, VP of Manufacturing Operations. "Loom Flow allows us to continuously reoptimize production based on current conditions, incoming orders, and equipment availability."
This dynamic approach enables much greater flexibility in production, allowing for efficient handling of both large runs and small-batch customization within the same facility—a capability that has been elusive in apparel manufacturing.
Loom Reach: Downstream Intelligence
Extending beyond the factory walls, Loom Reach provides downstream intelligence that enables feedback loops and demand sensing. This component integrates with e-commerce platforms, retail systems, and consumer data to provide insights that inform production decisions.
"The traditional model is to produce based on forecasts that are often wrong," noted Kaia Rhodes, Founder and CEO. "Loom Reach allows us to produce based on actual demand signals, reducing overproduction and ensuring we're making what consumers actually want."
The system can identify emerging trends, track product performance, and even predict future demand based on a variety of signals. This intelligence feeds back into production planning, creating a closed loop that continuously improves accuracy and efficiency.
Loom Chain: Supply Chain Visibility
Completing the platform is Loom Chain, which provides unprecedented visibility and traceability across the supply chain from raw materials to finished products. This component tracks the journey of materials and products through every stage of production and distribution.
"In an industry plagued by opacity, Loom Chain creates transparency," said Rhodes. "Brands and consumers can see exactly where materials came from, how products were made, and how they moved through the supply chain."
This visibility is increasingly important for brands concerned about sustainability, ethical production, and supply chain resilience. It also enables more efficient inventory management and logistics planning.
Integration and Deployment
While each component of Loom OS addresses specific challenges, their integration into a cohesive platform creates capabilities greater than the sum of their parts. The system is designed to be deployed in Anatar's own manufacturing facilities as well as potentially licensed to other manufacturers in the future.
"We're building Loom OS to power our own production first and foremost," explained Rhodes. "But we recognize that transforming the industry requires broader adoption of these technologies, so we're designing with eventual licensing in mind."
The initial deployment of Loom OS will be in Anatar's forthcoming Georgia manufacturing facility, where it will orchestrate production across the company's first autonomous line. As the system proves its capabilities, Anatar plans to expand both its own manufacturing footprint and potentially the availability of the software to strategic partners.
"This is just the beginning," concluded Chen. "Loom OS will continuously evolve based on operational data and emerging technologies. We're building a learning system that gets better with every garment produced."
For more information about Loom OS and Anatar's approach to modern apparel manufacturing, visit anatar.com/platform.