The Environmental Impact of Reshoring Apparel Production
How domestic manufacturing can reduce carbon footprints and waste in the apparel industry
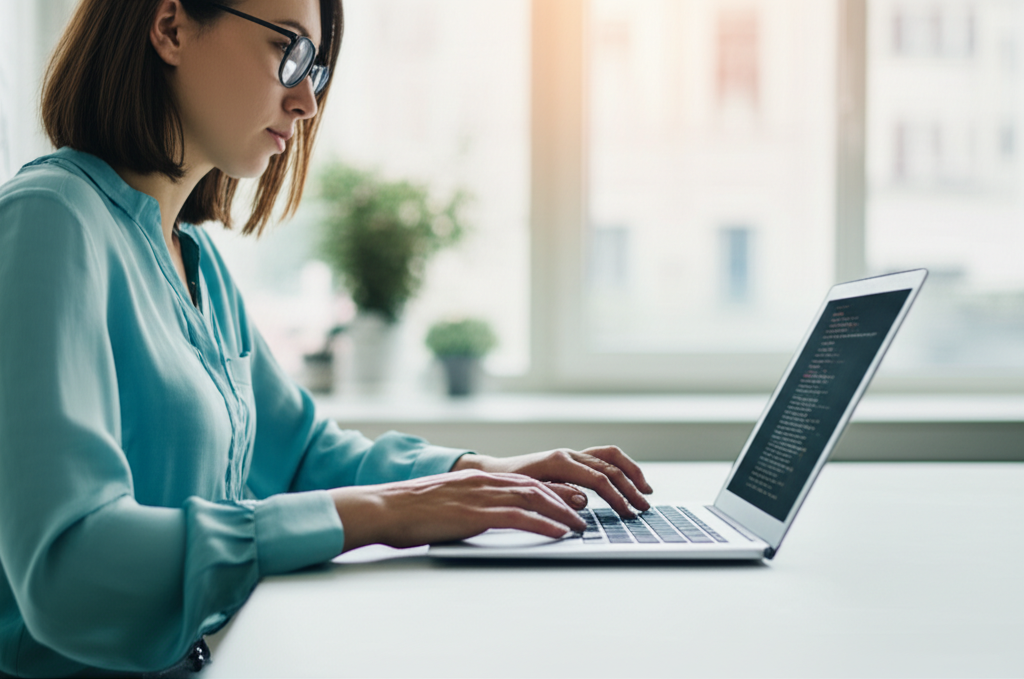
Sarah Johnson
Technology Writer & Industry Analyst
The environmental footprint of the global apparel industry is staggering. From the carbon emissions associated with shipping garments across oceans to the water pollution from dyeing and finishing processes, clothing production ranks among the world's most environmentally intensive industries. However, the emerging trend of reshoring—bringing manufacturing back to domestic markets—offers promising environmental benefits that could help address these challenges.
Transportation Emissions: The Hidden Cost of Global Supply Chains
One of the most obvious environmental benefits of reshoring is the dramatic reduction in transportation emissions. When a t-shirt is manufactured in Bangladesh and shipped to the United States, it typically travels over 8,000 miles, generating significant carbon emissions in the process.
"Transportation accounts for approximately 10% of the carbon footprint of a typical garment," explains Sarah Johnson, an industry analyst specializing in sustainable manufacturing. "By producing domestically, brands can eliminate most of these emissions, particularly the high-impact air freight often used for time-sensitive fashion items."
Anatar, a company building AI-powered apparel manufacturing facilities in the United States, estimates that domestic production can reduce transportation-related carbon emissions by up to 95% compared to overseas manufacturing.
Reduced Overproduction and Waste
Perhaps even more significant than transportation emissions is the potential for reshoring to reduce overproduction—a persistent problem in the industry. Long lead times associated with offshore manufacturing force brands to produce based on forecasts made months in advance, often resulting in excess inventory that ends up discounted, liquidated, or even destroyed.
"When you're producing 6-12 months in advance, you're essentially guessing what consumers will want," notes Kaia Rhodes, Founder and CEO of Anatar. "Our approach enables production much closer to the point of sale, allowing brands to produce smaller batches and replenish based on actual sales data."
This shift from "push" to "pull" manufacturing can significantly reduce waste. Industry studies suggest that approximately 30% of apparel produced globally is never sold at full price, representing massive resource waste. Domestic production with shorter lead times could potentially halve this figure.
Water Usage and Pollution
Apparel manufacturing is water-intensive, particularly in dyeing and finishing processes. Many traditional manufacturing countries have limited environmental regulations, resulting in significant water pollution from textile operations.
"In the U.S., we have much stricter environmental regulations governing water usage and discharge," explains Amara Washington, VP of Manufacturing Operations at Anatar. "Our facilities are designed to minimize water usage through closed-loop systems and advanced dyeing technologies that reduce both consumption and pollution."
These technologies include waterless dyeing processes, advanced filtration systems, and water recycling capabilities that can reduce water usage by up to 90% compared to conventional methods. When implemented at scale, these approaches could significantly reduce the industry's impact on water resources.
Energy Efficiency and Renewable Power
Modern manufacturing facilities in the United States typically have greater energy efficiency than their counterparts in developing countries. Additionally, they have more options for incorporating renewable energy into their operations.
"Our facility design incorporates solar power generation, energy-efficient equipment, and smart systems that optimize energy usage based on production needs," says Washington. "We're aiming for carbon-neutral operations within five years."
This focus on energy efficiency and renewable power can substantially reduce the carbon footprint of manufacturing operations. When combined with the transportation savings of domestic production, the overall climate impact of reshored manufacturing can be significantly lower than traditional offshore production.
Circular Economy Opportunities
Perhaps the most transformative environmental benefit of reshoring is the potential to enable more circular production models. When manufacturing occurs closer to the point of consumption, it becomes more feasible to recapture and reuse materials at the end of a product's life.
"We're designing our systems with circularity in mind," explains Rhodes. "Our vision includes not just producing new garments but eventually being able to take back worn items, disassemble them, and reincorporate the materials into new products."
This closed-loop approach could dramatically reduce the industry's resource consumption and waste generation. While true circularity remains challenging, the proximity of domestic manufacturing makes it much more achievable than in fragmented global supply chains.
Challenges and Considerations
Despite these potential benefits, reshoring is not automatically more sustainable. Domestic manufacturing must be designed with environmental performance as a priority to realize these advantages.
"Simply moving production to the U.S. without addressing fundamental process efficiency and resource usage won't solve the environmental challenges," cautions Johnson. "The key is combining reshoring with technological innovation that reimagines how apparel is produced."
Companies like Anatar are focusing on exactly this combination—leveraging automation, AI, and advanced materials to create manufacturing systems that are not just domestically located but fundamentally more sustainable in their operation.
The Path Forward
As reshoring gains momentum in the apparel industry, its environmental implications will become increasingly important. Brands and manufacturers have an opportunity to design these new domestic supply chains with sustainability as a core principle rather than an afterthought.
"We're at an inflection point where we can reimagine not just where apparel is made, but how it's made," concludes Rhodes. "By bringing production back to the U.S. and simultaneously reinventing the manufacturing process, we can create a model that's better for business, workers, and the planet."
This reimagining of apparel manufacturing represents one of the most promising paths toward reducing the industry's environmental footprint—a goal that grows more urgent as the climate crisis intensifies and resource constraints tighten.