The Economic Case for Reshoring Apparel Manufacturing
How technology is closing the cost gap and making American-made clothing competitive again
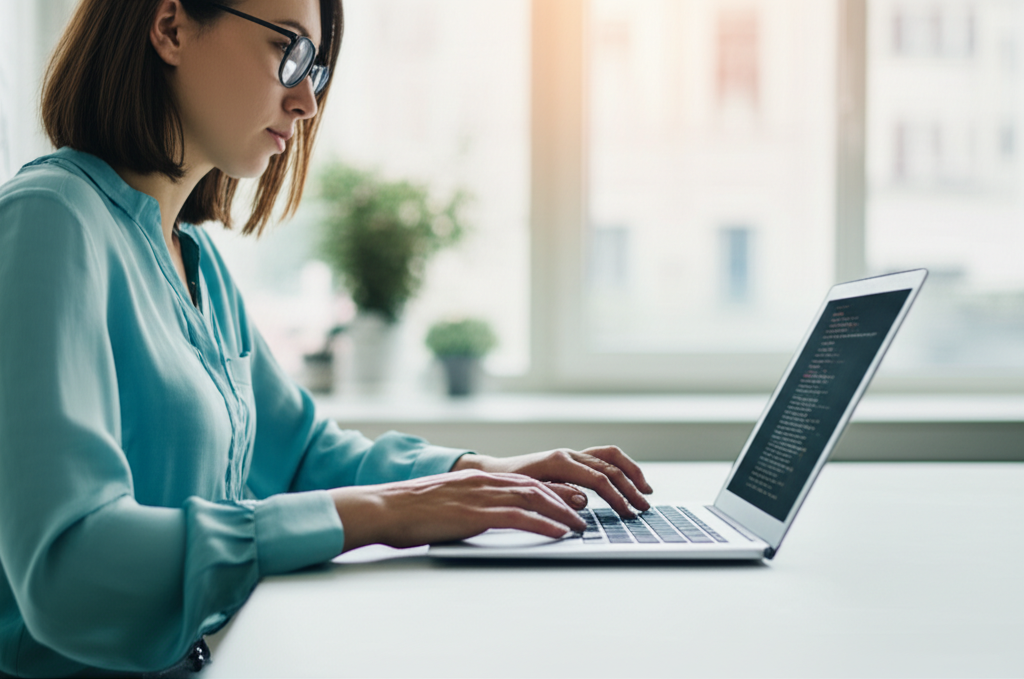
Sarah Johnson
Technology Writer & Industry Analyst
For decades, conventional wisdom has held that apparel manufacturing in the United States is economically unfeasible. With labor costs significantly higher than those in countries like Bangladesh, Vietnam, and China, the economics simply didn't work. This reality led to the offshoring of 97% of America's apparel production and the loss of over 90% of jobs in the sector.
However, a new economic equation is emerging—one that makes a compelling case for reshoring apparel manufacturing to the United States. At the heart of this shift is the dramatic reduction in labor costs achieved through automation and artificial intelligence.
Closing the Labor Cost Gap
"Automation can reduce labor costs by up to 90%," explains Kaia Rhodes, Founder and CEO of Anatar, a company building AI-powered apparel manufacturing facilities in the United States. "This fundamentally changes the math that drove manufacturing offshore in the first place."
Traditional apparel manufacturing is highly labor-intensive, with human workers performing most cutting, sewing, and finishing operations. In contrast, modern automated systems can handle many of these tasks with minimal human intervention, dramatically reducing the labor component of production costs.
When labor represents a smaller percentage of overall costs, the wage differential between the U.S. and traditional manufacturing countries becomes less significant. Other factors begin to weigh more heavily in the economic equation.
The Hidden Costs of Offshoring
The sticker price of offshore manufacturing has always masked numerous hidden costs that erode its apparent economic advantage:
- Long lead times: Offshore production typically requires 3-6 months from order to delivery, tying up capital and limiting responsiveness to market changes.
- Inventory costs: Longer lead times necessitate larger inventory buffers, increasing carrying costs and the risk of markdowns.
- Quality control challenges: Distance makes quality oversight difficult, often resulting in higher defect rates and returns.
- Transportation costs: Shipping containers from Asia to the U.S. adds significant expense, especially with rising fuel costs and port congestion.
- Compliance and monitoring: Ensuring ethical manufacturing practices requires substantial investment in monitoring and compliance programs.
"When you factor in all these hidden costs, the apparent savings from offshore manufacturing shrink considerably," notes Rhodes. "Add in the ability to respond quickly to market trends with short-run production, and suddenly domestic manufacturing becomes not just viable but advantageous."
The Market Premium for Made in USA
Another factor strengthening the economic case for reshoring is consumer willingness to pay a premium for American-made products. According to research, 77% of American consumers prefer products made in the USA, and many are willing to pay 10-15% more for them.
This premium reflects not just patriotic sentiment but also perceptions of higher quality, better labor standards, and environmental responsibility. For brands, this translates to higher margins that can offset any remaining cost differential in production.
Strategic and Resilience Benefits
Beyond direct economics, reshoring offers strategic benefits that have become increasingly apparent in the wake of supply chain disruptions caused by the pandemic, geopolitical tensions, and climate events.
"The ability to produce domestically provides a hedge against global supply chain disruptions," explains Amara Washington, VP of Manufacturing Operations at Anatar. "Brands that can source locally can maintain continuity of supply even when global shipping is disrupted."
This resilience has real economic value, as stockouts and missed market opportunities can cost far more than the marginal savings from offshore production.
The Path Forward
While the economic case for reshoring is strengthening, significant investment in infrastructure and technology is required to rebuild America's apparel manufacturing capacity. Companies like Anatar are leading this charge by developing vertically integrated manufacturing facilities powered by advanced robotics and AI.
"We're building the infrastructure for a new era of American apparel manufacturing," says Rhodes. "Our approach combines the best of technology with strategic human expertise to create a model that's economically competitive and scalable."
As these new manufacturing models prove their economic viability, they could catalyze a broader reshoring movement. The result would be not just a revitalized industry but also the creation of new, high-skilled jobs and a more resilient supply chain for a sector that touches every American consumer.
The economics that drove apparel manufacturing offshore haven't disappeared, but they've been fundamentally altered by technology. For the first time in decades, the numbers are starting to favor American production—a shift with profound implications for the industry and the economy at large.